Rebuild of an adhesives plant following a factory fire
The Company
Established in 1890, Caswell Adhesives have earned a reputation as a leading independent adhesives manufacturer, offering a range of hot melt adhesives and glues, together with a comprehensive range of tailor-made products for a wide range of industries, both in the UK and overseas.
Their site in Corby manufactures hot melt, water-based, PU and MS adhesives.
Project Brief
A major fire had destroyed Caswell Adhesives’ production plant and resulted in a move into a temporary manufacturing unit. Ai Process were appointed to successfully restore the plant in Corby, East Midlands, to full production. The new facility needed to provide Caswell Adhesives the flexibility to offer its customers bespoke adhesive products whilst also allowing for an increase in production of their regular product ranges.
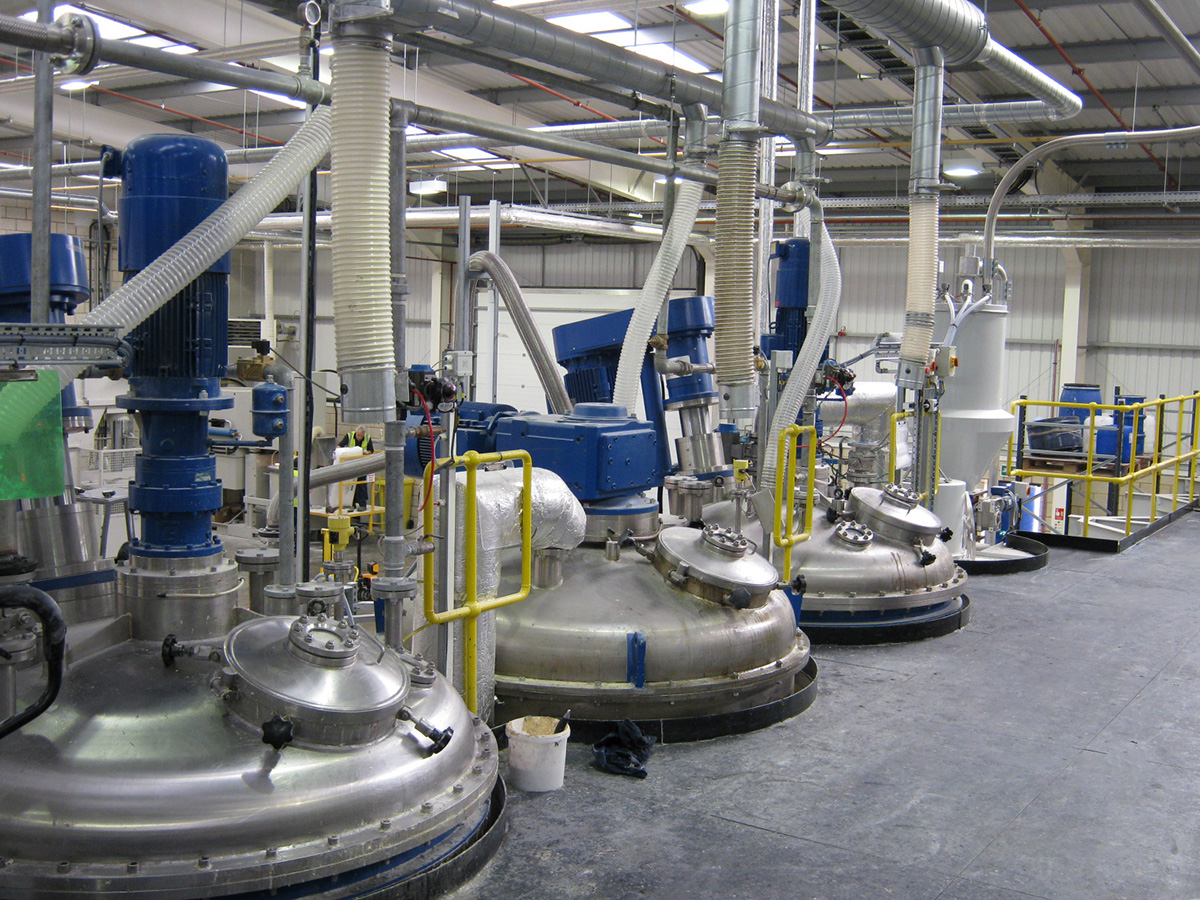
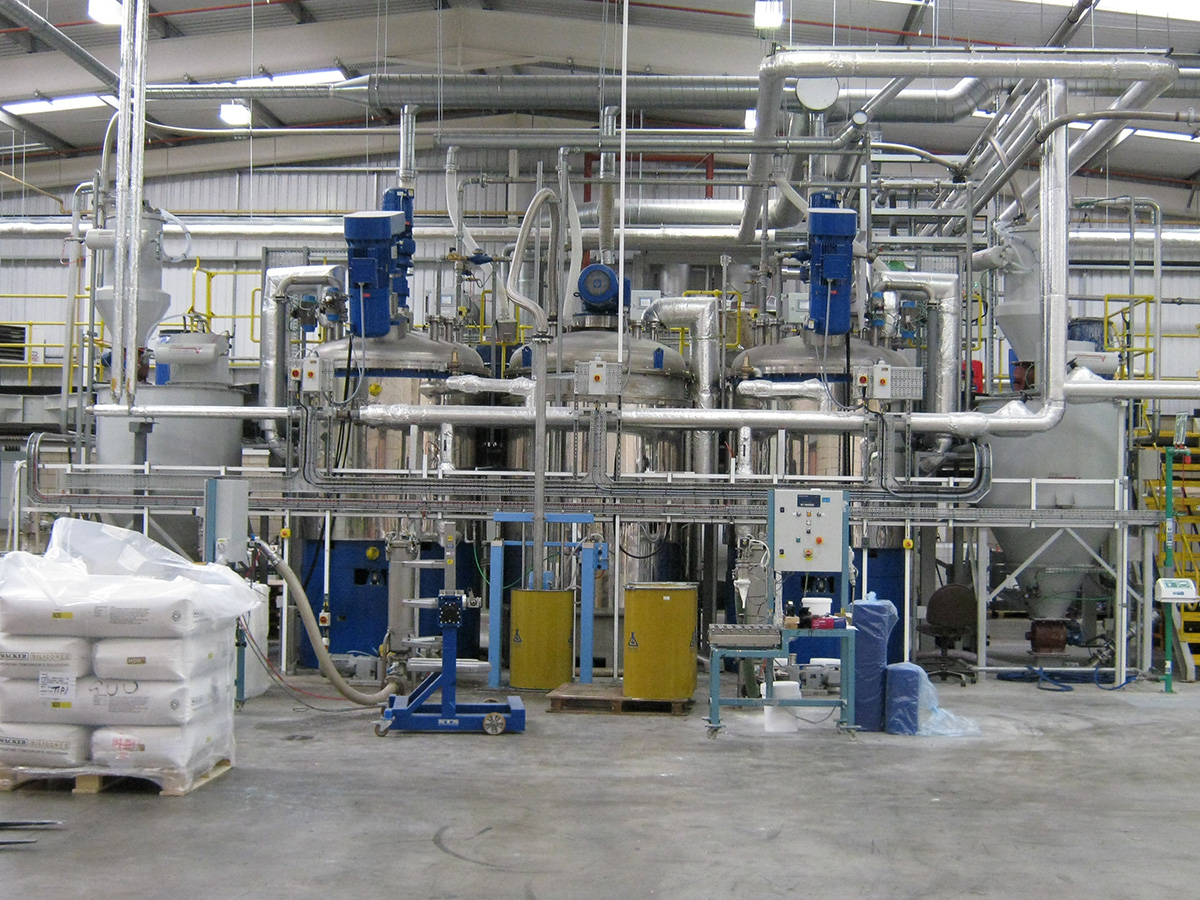
Scope of Works
The project requirements included process design, construction and installation of:
- A new bulk powder and liquid tank farm
- Prime manufacturing equipment
- Filling and packaging lines
- A recipe driven SCADA control system
- Infrastructure including new mezzanine floors, pipework, trace heating, lagging and cladding, electrics and extraction
The project also included the relocation of equipment from a temporary site to their new production facility.
Design Challenge
To restore and improve full manufacturing capability to the site in the shortest possible time, whilst giving consideration to:
- Process flow
- Operator footfall
- Maintenance access
- Health and safety regulations
- Additional capacity for future growth
Time was of the essence given that, each day after the fire, Caswell Adhesives were unable to meet the ever-increasing demands from their customers.
Testimonial
A major part of this project was to ensure that all the health and safety aspects had been considered. Following the effects of the fire, it was imperative that all operations were suitably risk assessed and acted upon.
Alan Parry
Ai Process